Le traitement des matières premières
La céramique vient du mot “keramos” qui signifie argile. C’est, avec le verre et l’émail, l’une des composantes des “arts du feu”, car l’intervention du feu modifie la matière de façon irréversible. La céramique se décompose en quatre grandes familles : la poterie, la faïence, le grès et la porcelaine. Sa préparation se répartit autour de quatre grandes étapes. La préparation de la pâte, son façonnage ou modelage, sa décoration et sa cuisson. Les matières premières constituées de terres argileuses sont broyées avec de l’eau. Depuis le XXe siècle, on utilise des broyeurs à galets. Ces broyeurs ont succédé aux moulins à meules de grès. Ces machines permettent d’obtenir la finesse du grain souhaitée. La matière obtenue est filtrée puis pressée dans des filtres-presse. La terre subit ensuite une dernière opération : le désaérage. Il permet d’éliminer toutes les bulles d’air qui auraient pu rester à l’intérieur de la terre ou de la pâte. Cette opération se faisait autrefois avec les pieds, d’où le nom de l’atelier de “marche à pâte” encore conservé dans quelques manufactures qui fabriquent elles-mêmes leur pâte. Cette dernière sort de la machine sous forme de “boudins”, qui sont ensuite découpés en petites galettes rondes appelées “camemberts”. La terre est alors prête à être façonnée.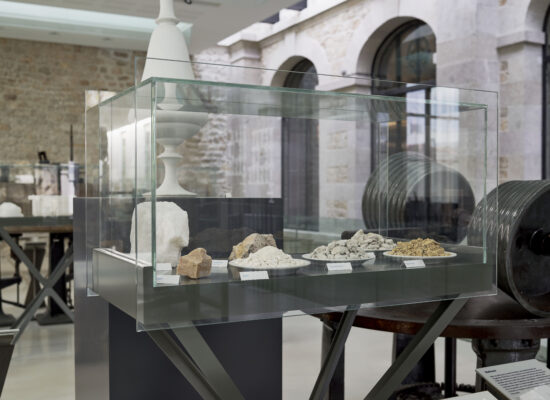
Le façonnage
L’artisan peut se servir d’un tour ou utiliser la technique du moulage, soit par pressage, soit par coulage. Jusqu’à une époque récente, les moules étaient en plâtre, mais celui-ci est peu à peu remplacé par des matières synthétiques. Depuis la deuxième moitié du XIXe siècle, on se sert de la porosité du plâtre pour fabriquer les objets les plus fins par coulage. La pâte à porcelaine est alors liquéfiée et versée dans un moule. Par capillarité, l’eau contenue dans la pâte pénètre dans le plâtre, provoquant le durcissement progressif des bords. Dès que l’on a obtenu l’épaisseur voulue, on rejette le surplus de la pâte appelée dans ce cas “barbotine”.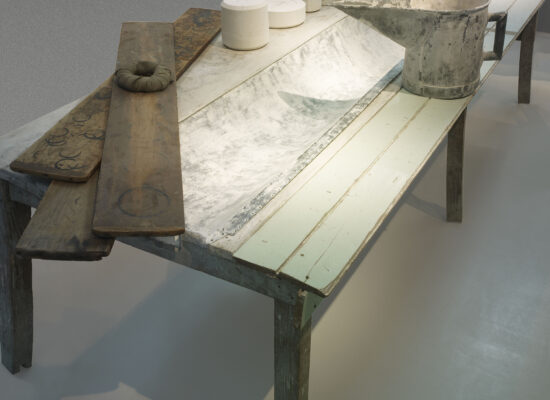
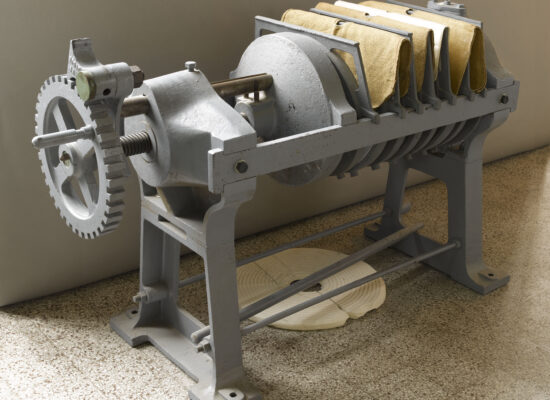
La décoration
La polychromie est obtenue grâce à des oxydes métalliques : chaque oxyde donne une ou plusieurs couleurs après cuisson. Les oxydes de base sont le cobalt, qui produit le bleu, le cuivre, qui peut se transformer en vert ou en turquoise, le fer, qui peut donner du jaune ou du rouge, le manganèse, qui donne les bruns ; le rose ou pourpre est obtenu avec du chlorure d’or. Jusqu’au XVIIIe siècle, le décor est appliqué au pinceau. Au XIXe siècle, dans un souci d’industrialisation, on utilise les techniques de l’imprimerie à taille-douce qui permettent, grâce à une plaque de cuivre, l’impression d’un décor monochrome. Ce décor monochrome est rehaussé à la main avec des couleurs (“enluminures”). La chromolithographie remédie à cet inconvénient par l’impression d’un décor au moyen d’un nombre de pierres équivalent au nombre de couleurs souhaitées. Cette technique, très bien maîtrisée à la fin du siècle, permet l’emploi d’une palette de dix-huit couleurs. La décalcomanie moderne recourt à la sérigraphie qui est basée sur le même principe mais à l’aide d’écrans de soie, puis de matières synthétiques. Pour appliquer le décor, on utilise deux méthodes. La première est appelée décor de grand feu. La seconde est appelée décor de petit feu.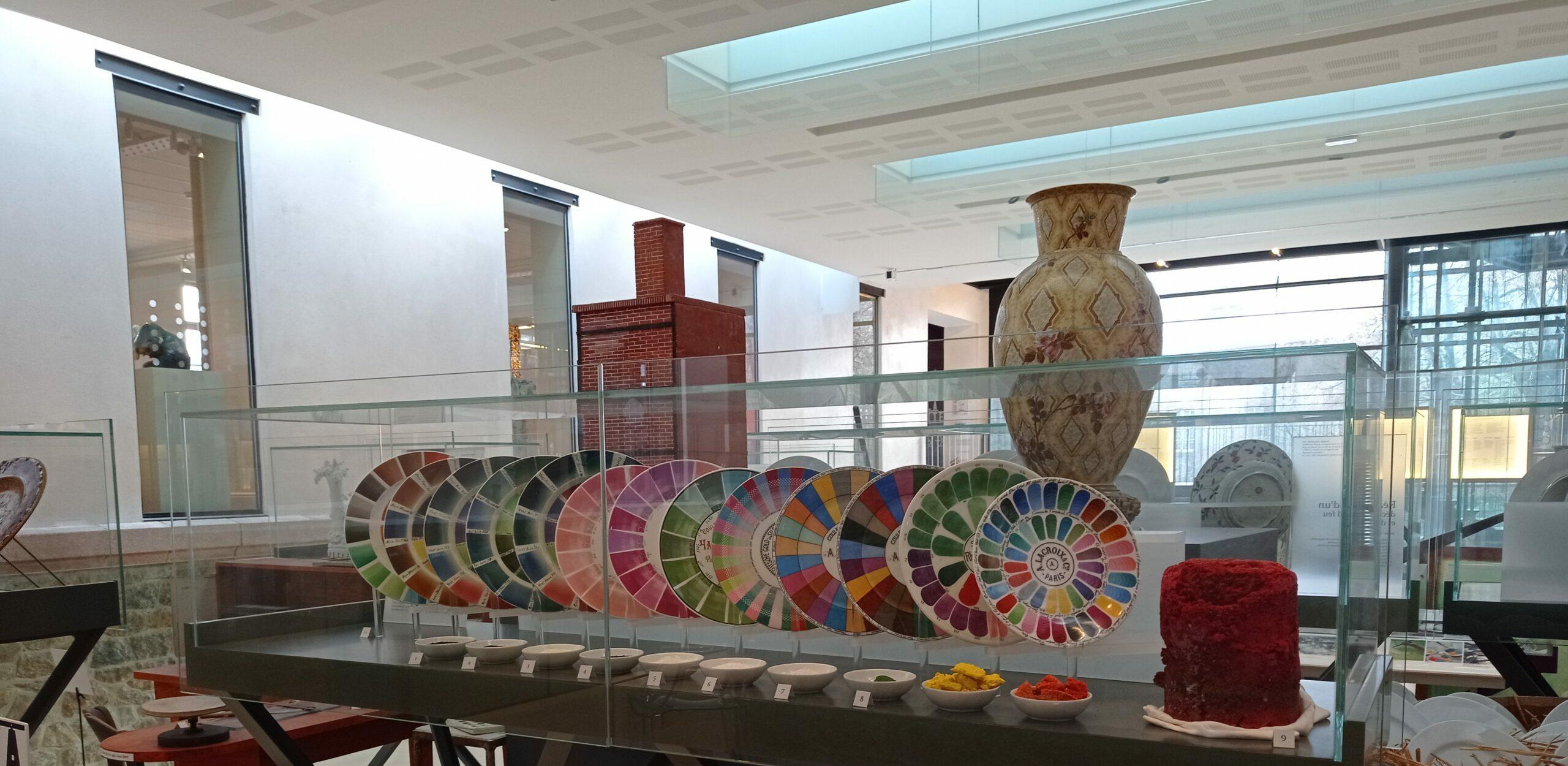
La cuisson
La cuisson d’une céramique se singularise par son irréversibilité absolue. Avant d’être décorés, les objets subissent une première cuisson dite de “dégourdi”, à 900°, dont le but est de sécher l’objet déjà façonné, avant d’être émaillé. La cuisson de la porcelaine dure doit atteindre 1400°. Dès le XVIIIe siècle, on élabore des fours capables d’atteindre cette température. On met au point à Sèvres dès 1769 des fours ronds. Initialement ces fours fonctionnent au bois. À partir des années 1850, on les alimente au charbon. Dans les années 1960, la cuisson au gaz se généralise. L’installation des pièces dans le four est délicate. Afin d’empêcher l’affaissement des objets en porcelaine, on les place dans des étuis en terre réfractaire ou “gazettes” qui sont ensuite facilement empilés. La cuisson contemporaine au gaz diminue considérablement les aléas de la déformation, des tâches, voire de la casse.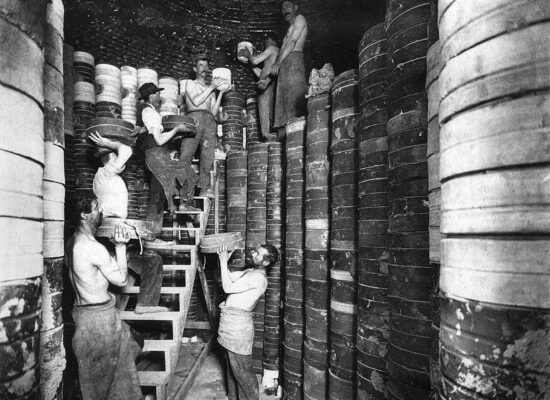